Manual Assembly#
As study cases for the manual assembly, we fabricated:
a roof structure detail connected with half-lap scarf joints and half-lap cross joints that were manually fabricated with Augmented Reality (AR) assistance and assembled with the aid of standard construction tools and equipment.
a frame structure with four wood logs connected with half-lap cross joints
Steps#
1. Input the data#
First things first, let’s import your cleaned scan and corresponding polysurface model in Rhino.
2. Build the DFAssembly#
Here we convert the model of our structure into the internal datatype of diffcheck, DFAssembly.
Hint
If you are evaluating round sections e.g. logs, you can set the i_is_roundwood
input to True
in the DFBuildAssembly
component.
DF’s components:
3. Registration of CAD and scan#
The registration is the process of aligning the CAD model with the scan. This is done by selecting corresponding points on the CAD model and the scan and find a transformation that minimizes the distance between them.
4. Segmentation of the scan#
Once the scan and the CAD model are aligned, we can segment the scan to isolate the parts of the raw point cloud of the scan that corresponds tothe joints.
DF’s components:
5. Error computation#
At this point we can compute the error between the CAD model and the scan. The error is computed as the distance between the closest point on the CAD model and the scan. The current DF’s output metrics are:
distance : the distance between the closest point on the CAD model and the scan
mean : the mean distance between the closest point on the CAD model and the scan
max_deviation : the maximum distance between the closest point on the CAD model and the scan
min_deviation : the minimum distance between the closest point on the CAD model and the scan
std_deviation : the standard deviation of the distance between the closest point on the CAD model and the scan
DF’s components:
6. Error Visualization#
DF allows you to quickly visualize the errors in the Rhino viewport. The color of the points represents the distance between the CAD model and the scan. The color scale can be adjusted to better visualize the error. We also provide a graph that shows the distribution of the errors.
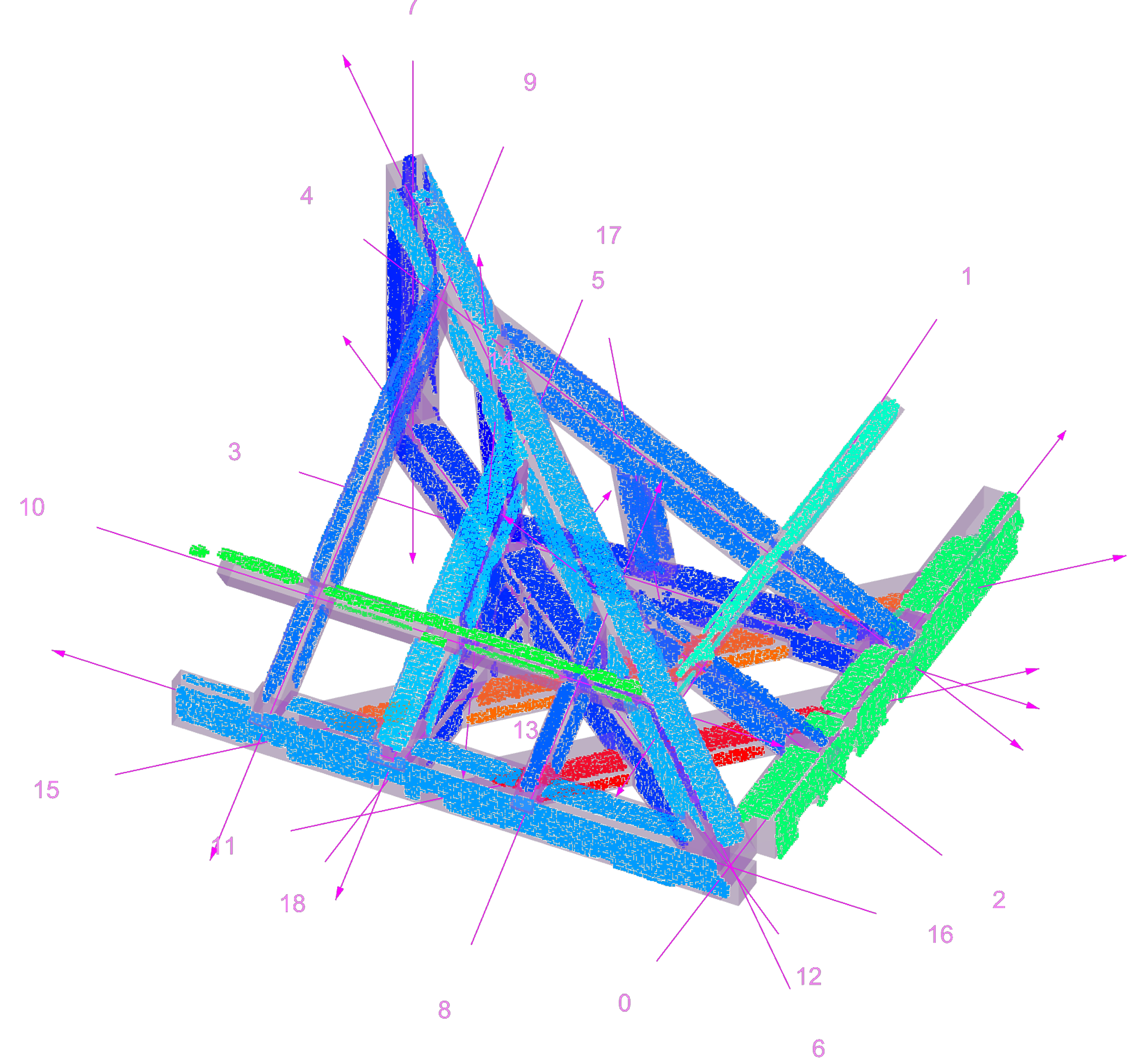
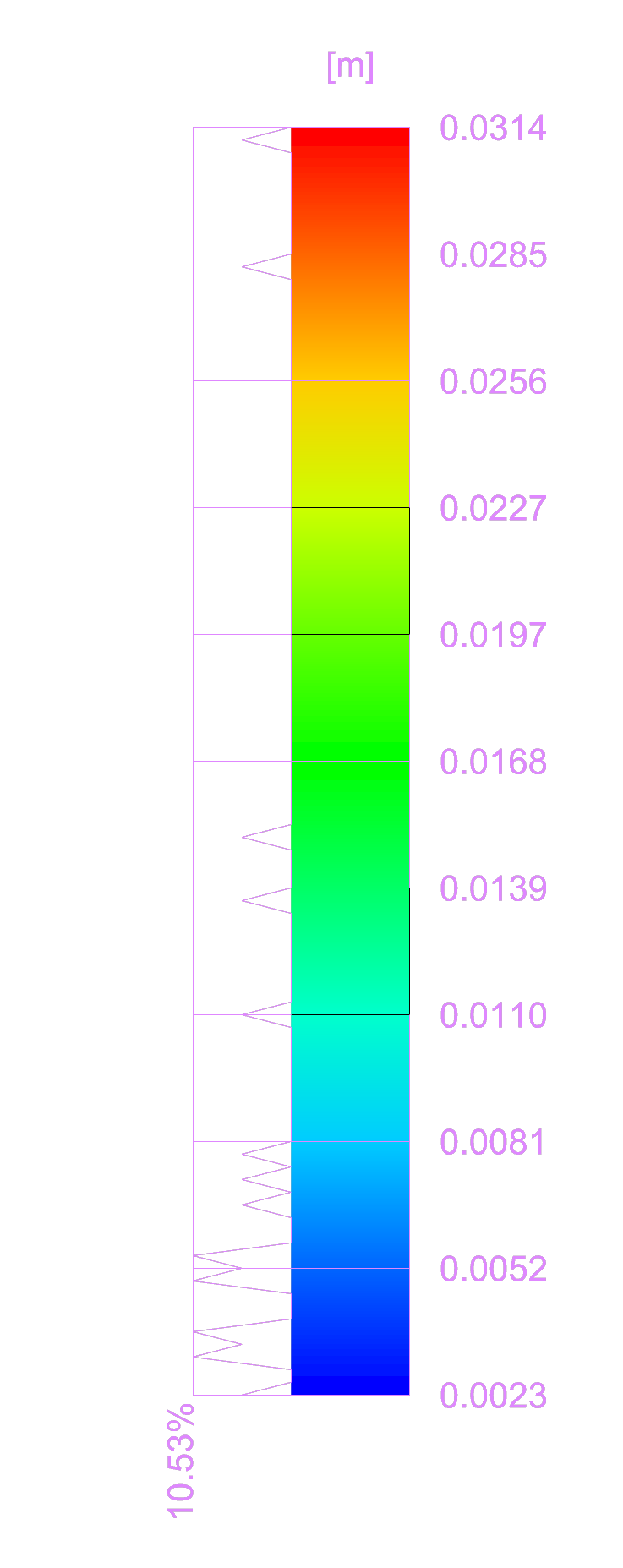
DF’s components:
7. Export the results#
The results can be also exported in a CSV file for further analysis or documentation.
The CSV contains the values per element for the Roof Case Study (1)..
Beam ID |
Min Deviation |
Max Deviation |
Std Deviation |
RMSE |
Mean |
---|---|---|---|---|---|
0 |
0.0001 |
0.0899 |
0.0103 |
0.0171 |
0.0137 |
1 |
0 |
0.0263 |
0.0075 |
0.0134 |
0.0112 |
2 |
0 |
0.0176 |
0.0044 |
0.0068 |
0.0052 |
3 |
0 |
0.0258 |
0.0030 |
0.0048 |
0.0037 |
4 |
0 |
0.0192 |
0.0092 |
0.0072 |
0.0057 |
5 |
0 |
0.0711 |
0.0046 |
0.0061 |
0.0053 |
… |
… |
… |
… |
… |
… |
and for the Frame Case Study (2)..
Beam ID |
Min Deviation |
Max Deviation |
Std Deviation |
RMSE |
Mean |
---|---|---|---|---|---|
0 |
0 |
0.1066 |
0.0147 |
0.0202 |
0.0139 |
1 |
0 |
0.1448 |
0.0158 |
0.0214 |
0.0144 |
2 |
0 |
0.1155 |
0.024 |
0.0402 |
0.0323 |
3 |
0 |
0.103 |
0.0198 |
0.0333 |
0.0267 |
DF’s components: